Comprehensive Guide for ISA 95 Integration of Enterprise and Control Systems ISO 62264
- Emrah Demirezen
- Nov 26, 2024
- 4 min read
1. Overview of ISA-95
ISA-95, also referred to as IEC/ISO 62264, is an international standard that establishes a framework for the seamless integration of enterprise systems, such as Enterprise Resource Planning (ERP), with control systems, such as Manufacturing Execution Systems (MES). The objectives of this standard include:
Bridging the gap between enterprise and manufacturing systems.
Enhancing communication and interoperability.
Improving operational efficiency through process standardization.
Historical Context:
ISA-95 was established to address the growing demand for uniformity in the communication of manufacturing systems. Originally focused on industries such as pharmaceuticals and automotive, the standard has broadened its scope to encompass a variety of sectors, offering a dependable framework for optimizing data exchange and process synchronization.
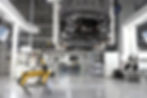
2. Objectives of ISA-95
Define Standardized Models:
Facilitate consistent terminology and a unified data model for system integration, reducing ambiguity across enterprise and manufacturing sectors.
Support Seamless Integration:
Develop a structured framework to integrate ERP, MES, and process control systems, ensuring efficient data transfer and minimizing errors.
Optimize Operations:
Enhance workflows, minimize manual interventions, and improve decision-making by providing timely and accurate data.
Facilitate Scalability:
Enable easy integration of new systems, machinery, and technologies, supporting future growth and innovation.
Enable Regulatory Compliance:
Ensure traceability, auditability, and adherence to industry standards, meeting regulatory requirements in highly controlled industries such as automotive and aerospace.
Overview of Primary Advantages:
Increased productivity achieved through standardization.
Better coordination among departments and systems.
Access to real-time production metrics for informed decision-making.
Lower operational costs by removing redundancies.
3. Core Concepts of ISA-95
3.1 Functional Hierarchy Model
ISA-95 organizes manufacturing activities into five distinct levels:
Level 0: The physical process (e.g., machines, sensors, and devices).
Level 1: Control systems for monitoring and manipulating processes (e.g., PLCs, SCADA systems).
Level 2: Supervisory systems (e.g., HMIs and data acquisition systems).
Level 3: Manufacturing operations management (MES and related systems).
Level 4: Business logistics and planning (ERP and supply chain systems).
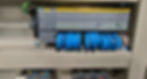
Detailed Example:
In a state of art facility, the Level 4 ERP system is responsible for managing production planning and procurement in alignment with demand forecasts. This ERP system communicates the production schedules to the Level 3 MES, which manages batch production activities. Levels 0-2 are tasked with ensuring compliance with stringent regulatory standards, facilitated by real-time monitoring of parameters such as temperature and pressure.
3.2 Models and Definitions
ISA-95 introduces standardized models to harmonize data and processes:
Activity Models: Define manufacturing functions like scheduling, quality control, and inventory management. For instance, the activity model A3 describes how production scheduling interacts with inventory tracking and material usage.
Object Models: Represent entities such as personnel, equipment, materials, and processes. Each object includes defined attributes, such as equipment capabilities, material properties, and personnel certifications.
Data Flow Models: Illustrate information exchange pathways between hierarchical levels.
Technical Insights:
Activity models map workflows, specifying inputs, outputs, and constraints.
Object models utilize attributes to create a uniform data structure for seamless integration.
3.3 Key Components
Personnel: Roles, responsibilities, and qualifications needed for production and maintenance.
Equipment: Specifications, performance metrics, and maintenance records for machinery and tools.
Material: Definitions of raw materials, intermediate products, and finished goods, including batch numbers and quality specifications.
Processes: Standardized workflows, such as production cycles, quality assurance procedures, and logistics operations.
Information: Real-time data (e.g., production rates) and historical data (e.g., past maintenance records) critical for decision-making.
4. ISA-95 Part Series
Part 1: Models and Terminology
Establishes the functional hierarchy and standard terminologies.
Defines foundational models for aligning enterprise and control systems.
Part 2: Object Models and Attributes
Provides detailed definitions for entities, including equipment, materials, and personnel.
Specifies attributes like equipment capacity, material composition, and personnel skills.
Part 3: Activity Models of Manufacturing Operations Management
Focuses on Level 3 activities, such as production scheduling, quality management, and inventory control.
Models activities using predefined templates to ensure consistency.
Part 4: Object Models for Manufacturing Operations Management
Extends object models to represent operational specifics, like material flow, storage locations, and production batches.
Includes detailed schemas for managing complex manufacturing processes.
Part 5: Business-to-Manufacturing Transactions
Defines transaction standards for exchanging data between ERP and MES systems.
Covers protocols for secure and reliable communication, ensuring data integrity.
5. Detailed Implementation Steps
Step 1: Assessment
Conduct a comprehensive audit of current systems, identifying integration gaps and inefficiencies.
Step 2: Define Objectives
Establish clear KPIs, such as improving on-time delivery rates or reducing production cycle times.
Step 3: Develop a Roadmap
Use ISA-95’s activity and object models to map out integration plans and milestones.
Step 4: Align Data Structures
Leverage ISA-95 object models to standardize data formats and terminology across systems.
Step 5: Build Interfaces
Implement middleware solutions to facilitate data exchange between ERP and MES systems.
Step 6: Validation and Testing
Perform rigorous testing to ensure the accuracy and reliability of integrated systems.
Step 7: Training
Educate stakeholders on ISA-95 frameworks and new workflows.
Step 8: Monitor and Optimize
Continuously evaluate integration outcomes, identifying areas for improvement.
6. Benefits of ISA-95
Interoperability: Seamless data flow between enterprise and control systems.
Efficiency: Automation reduces manual interventions and errors.
Scalability: Modular design supports expansion and modernization.
Data Consistency: Reliable data exchange ensures accuracy.
Compliance: Facilitates traceability and adherence to industry regulations.